We, we, we, we made it!

"These build journal entries are part of a Special Series on the development of the S85 CSL Style Carbon Plenum and S85 CSL Competition Complete Carbon Intake System.
In this entry, I cover my unboxing impressions and take a dive into the final tuning made on my pre-production unit that have made their way onto the production versions."
- Matt
BMW M made a prototype.
In the previous entry to this special series, I covered how BMW M engineered a one-off prototype with no regards for commercial use.
Fitting a 1 piece plenum over 120 degrees ITBs would result in an extremely high rate of installation errors leading to engine power limiting errors.
The engineering restrictions for ease of access and maintenance by dealerships was not a concern.
InfinityDesign made a commercial product.
InfinityDesign's main design philosophy was modularity, a topic we discussed in a previous journal entry.
In the development of the S85 CSL Carbon Plenum, Salman had to consider the ease of installing and uninstalling for common services.
It's no secret the S85 requires it share plenum-off maintenance like idle control actuators, throttle actuators, injectors and various other services that require the plenum to come off.
The pre-production unit:
a rough draft to build from.
The development process of the S85 CSL Carbon Plenum begun by the creation of the molds for the shells based on the 3D CAD designs.
This process was tedious, yet it was understood that the initial design would require further refinements by Salman himself to create the final production specifications.
The lower base and lid of the plenum of the plenums were first produced from the scans of the V10 engine's bay. These were considered the pre-production unit.
Below are pictures of the pre-production units.


Fine tuning from pre-production to production.
The production of the shells pales in comparaison to the fine tuning required to make a unit that would accommodate the performance requirements & numerous fittings needed for the MSS65 DME to bring the S85 to life.
These are the main improvements made from the pre-preproduction units to make the final production specs that will be delivered to the first 25x members who backed the crowdfunding earlier this Summer.
This is the unit I personally have and is displayed in pictures below.
Lower shell
The plenum lower shell has larger cut outs so that positioning velocity stack to throttle body boss is easier.
This is critical as it is expected for owners to be able to remove the stacks to change for the upcoming Motorsport variant trumpets and for regular servicing.
Removing the top lid may appear nerve racking, but it's pretty easy. Start slow with a ratchet. I used powered tools once bolts were loose to speed up the process.
You need to be mindful when re-bolting the lid to avoid threading the bolts and over-tightening with a power tool as it may scratch the clear coat.
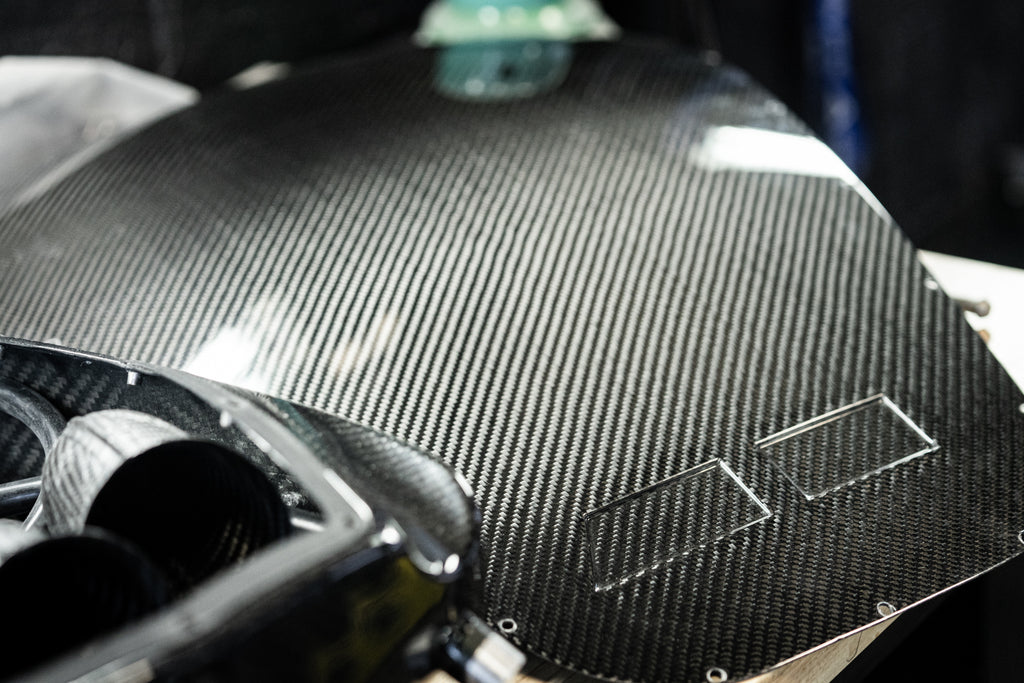
Plenum base can have further cut outs by end user for different trumpet alignment positions for the velocity stacks should they want OEM setup.
Oil Separators.
Oil separators are made from 1mm Pre Preg Carbon bonded into the lower shell of the plenum along with bonded barbed brass fittings going into silicone hoses.
The carbon fiber tubing is mounted in 3D Printed ASA with brass barbed fittings and is bonded to the lower shell surface with high temperature glue.
I'll take better pictures at install of the oil separators.

All the required fittings for PCV, vacuum and other components critical to the proper mechanical and electronic functioning of the air intake system are here.
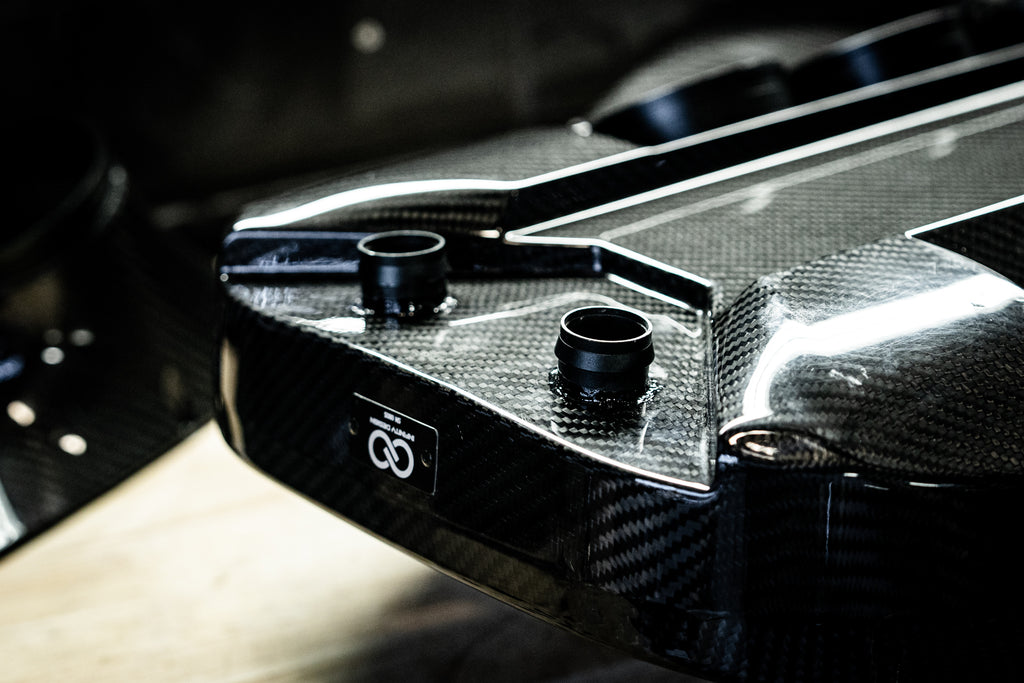

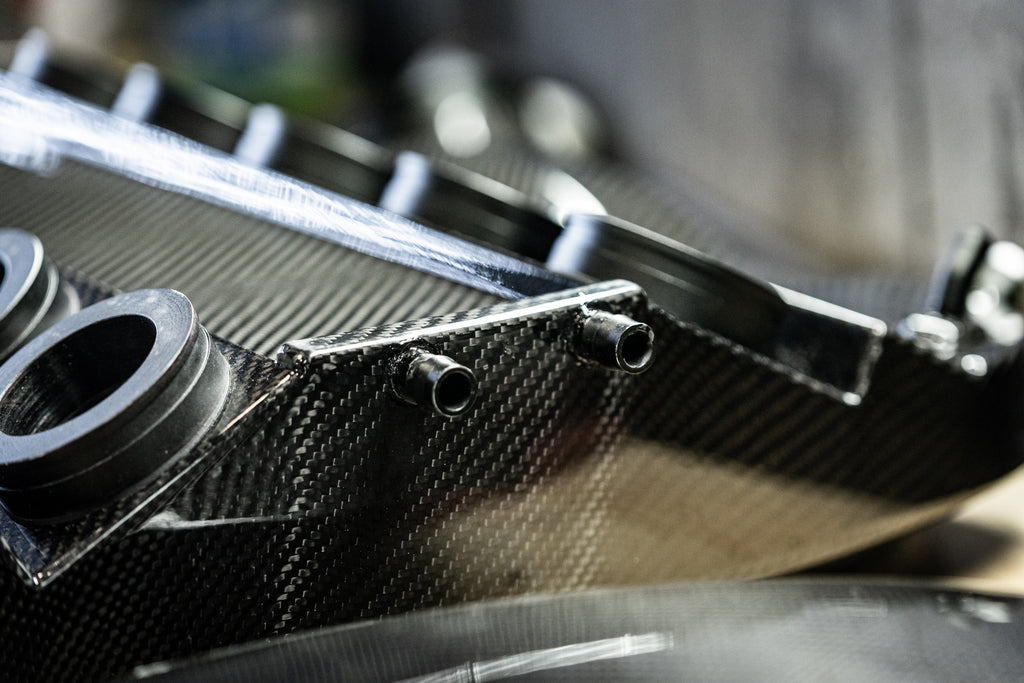
Neoprene Gaskets.
Sal opted to use Neoprene gaskets across the plenum. Neoprene is a much more durable material for gasket making than standard synthetic and natural rubber. It is tolerant to extreme conditions and temperatures of up to 500F / 260C.
The lower shell of the plenum has 2mm Neoprene flange fitted to ensure a perfect seal between the velocity stacks and the relatively rough internal surface of the lower shell's pre preg carbon.

Neoprene 2mm gaskets are further fitted to side inlets and top lid to ensure a tight seal all around.


The Throttle Body bosses are fitted with 2mm Neoprene Flanges to ensure perfect seal with smooth side outer carbon.

The design of the velocity stacks are based off OEM, with a slightly different positioning making use of the additional space created by the 1 piece design.


Velocity stacks.
The OEM+ velocity stacks have a 2mm aluminium base plates bonded to 1.5mm a carbon flange that structurally part of the velocity stack itself. The aluminum base is drilled to align perfectly with the throttle body boss threaded holes. This ensure a perfect internal wall alignment for smooth airflow, and no leaks.
Additionally, the carbon fiber trumpets are further reinforcement by additional carbon plies to eliminate cracking possibilities.
Improved Side Inlets.
The side lets were updated with thicker 3mm flange for easier fitment of neoprene gaskets and larger sealing surfaces.
Black hardware.
The modular design of the plenum evidently requires hardware. To retain clean aesthetics, Sal opted for black anodized hardware across the board.
It appears durable - this is a little detail that matters to me and I'll track as it gets used and abused.
This is the end of the piece-meal, it's time for cake.
Up next: it gets fitted, it gets driven, it gets recorded!